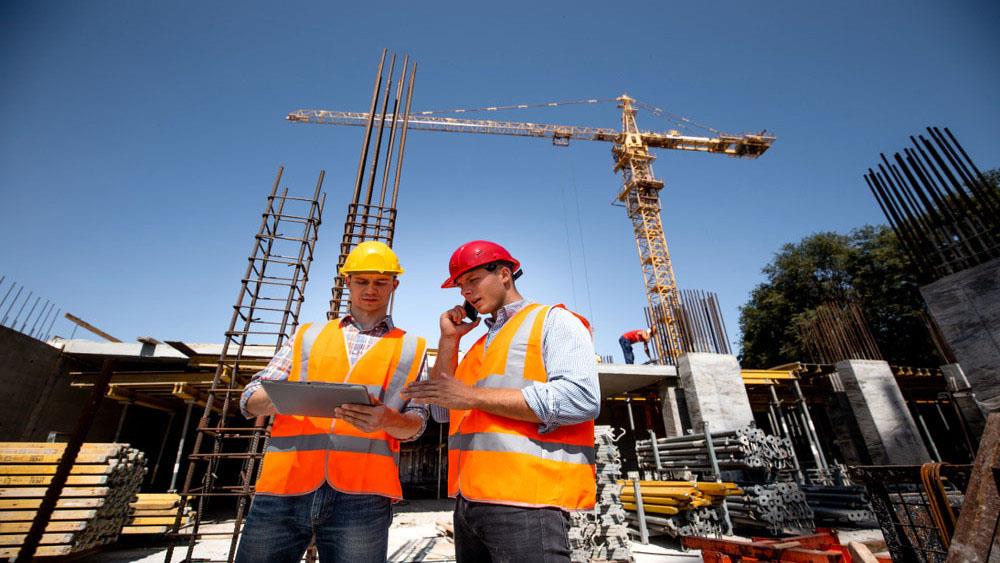
ONS data reveals which building materials are seeing the biggest rises in price and delivery time.
New research from Roofing Megastore reveals the enormous increase in both cost and lead times for many key building materials. The study analysed ONS data to examine the extent of the crisis, revealing which materials have been most impacted.
Timber supplies are by far the most affected, with prices increasing between 50-75% for many forms of structural timber. This is due to a combination of factors, with the perfect storm of Brexit and COVID-19 causing shifts in consumer behaviour, reduced staffing, and serious disruptions to supply chains.
Top 10 Building Materials Increasing in Price Year-on-Year October 2021:
YoY Increase (%)
1 Imported Sawn or Planed Wood 74%
2 Fabricated Structural Steel 73%
3 Particle Board 65%
4 Concrete Reinforcing Bars (Steel) 62%
5 Imported Plywood 56%
6 Builders’ Woodwork 14%
7 Plastic for Doors and Windows 13%
8 Pre-Cast Concrete Products 12%
9 Non-Aqueous Paint 11%
10 Flexible Pipes and Fittings 8%
This crisis comes alongside the Government’s ambitious targets for building new homes, as well as the health of an industry worth nearly £120 billion to the UK economy.
The Construction Leadership Council has warned that these shortages may persist until at least the end of the year, with many projects already delayed by months due to a lack of materials according to the Federation of Master Builders.
Prices across all aspects of building work have been affected by the materials shortages this year. Repair and maintenance work in the UK is the most affected with prices increasing by 26% in October 2021 compared to 2020, and new housing isn’t far behind, with prices increasing by more than 22%.
Increases in Project Costs Year-on-Year October 2021:
YoY Increase (%)
1 Repair & Maintenance 25.9%
2 All Work 23.5%
3 Other New Work 22.8%
4 New Housing 22.4%
From lockdown restrictions and business shutdowns to the current shortage of HGV drivers, the combination of COVID-19, Brexit, and overseas supplies shortages has left anyone taking on a building project feeling the effects.
Higher prices and longer delivery times on materials has caused many projects to continue well beyond their expected completion date, and left buyers in temporary accommodation for months while their new property is being built.
Changes in consumer behaviour and demand throughout the first lockdown are still having far-reaching effects. Protective screens in office and retail spaces for example, caused unprecedented demand for plastics such as polycarbonate sheets, which experienced nearly triple year-on-year demand in Spring and Summer 2020.
Other knock-on effects include a lack of raw materials due to disrupted supply chains and increased demand globally. For example, the global shortage of raw materials such as concrete has caused a 30% drop in the production of concrete roof tiles in Britain when compared to Q3 2020, and an even greater drop of 40% when compared to 2019.
As well as construction professionals, thousands of British homeowners have also felt the effects of these price increases. According to the ONS, the cost of building materials has increased by nearly 25% year-on-year, and nine out of ten small builders are having to delay projects due to the ongoing crisis according to a survey by the FMB. All of these factors together mean homeowners are having to wait even longer and pay much more for the same project when compared to 2019.
Gian-Carlo Grossi, Managing Director of Roofing Megastore, said: “As an online building supplies merchant, we’re all too aware of the effects these crises are having across the industry. For such a core sector of the economy, there needs to be significant co-operation between the Government and businesses within construction supply chains to resolve these issues as quickly as possible.”
The full research, including further information on the crisis can be found at: https://www.roofingmegastore.co.uk/2021-building-supplies-crisis