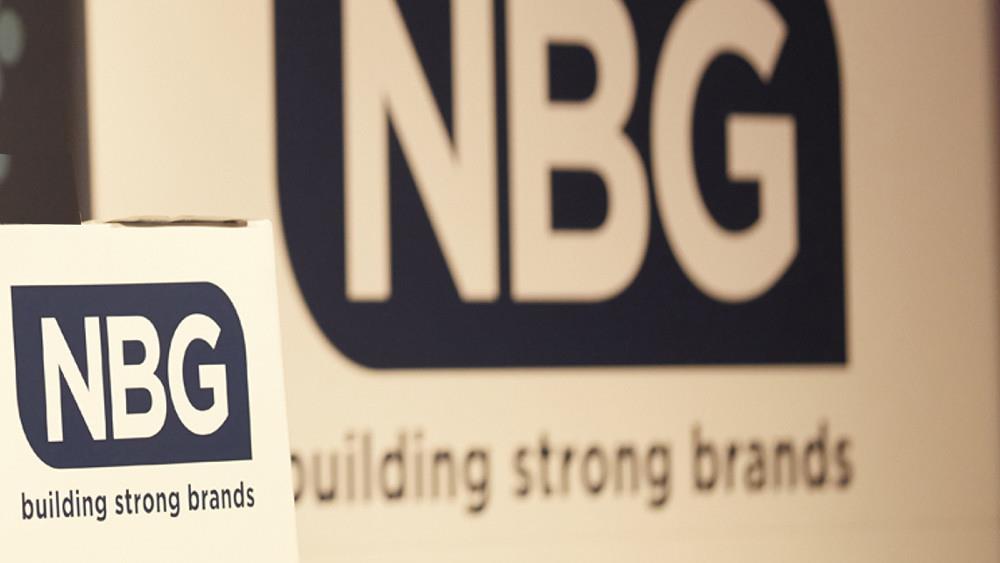
NBG has also confirmed imminent plans to release guidance documents for Partners and Suppliers on how to navigate the financial obligations around plastic packaging.
National Buying Group is to accelerate its talks with Suppliers as it steps up efforts to reduce plastic packaging in the construction supply chain and the potential tax impact on independent merchants.
The ongoing dialogue with Suppliers follows recent clarification of the obligated parties under the Department for Environment, Food and Rural Affairs’ Extended Producer Responsibility for packaging, which is expected to come into force in 2024.
Having realised that the original proposals risked placing onerous obligations on the merchant, it is now understood that DEFRA will consider a product’s supplier or brand owner, own label owner and importers as the obligated party or “Producer”.
The organisation deemed to have the greatest influence on the packaging they place on the UK market will now face the greatest cost penalties. Those Suppliers shipping products in plastic packaging and merchants opting to repackage product in their own branded packaging risk the greatest financial burden.
A recent NBG Sustainability and Cost Reduction Forum meeting, attended by both Partners and Suppliers, was given the results of an in-depth audit of a builder’s merchant that is facing a potential tax bill in excess of £75,000.
The same audit calculated that suppliers of plastic packaging to Kellaway could be set for an even greater increase of somewhere between a 10 and 30-fold increase on current prices. Using these figures, the audit calculated a potential jump from £3,000 in 2022 to a staggering £196,000 come 2024.
Bob Fleetwood, of Kellaway Building Supplies, who is leading NBG’s plastics reduction team along with Jasmine King from NBG’s Central Team, says the audit looked at all areas of the merchant’s activity, both indoors and in the yard, to build up a picture of what merchants are facing in terms of their tax liability.
The audit identified multiple areas that require further examination, including the use of plastic packaging for branding purposes, the potential over-use of stretch wrap to secure product to pallets and the use of dumpy bags for transporting aggregate.
“The audit looked at everything from hand tools to roofing felt, insulation and timber along with all packaging types from branded packaging to bubble wrap, stretch and shrink wrap,” said Fleetwood.
“We now need to understand why manufacturers of building products use plastic packaging, what alternatives can be put in place, such as recycled plastic packaging and, perhaps most importantly, where it can be eliminated altogether with no impact on product quality, transportation or merchant yard safety."
Plastic remains the most commonly used packaging for construction products and is being targeted by HMRC’s Plastic Packaging Tax, which came into force on the 1 April 2022. The tax applies a charge of £200 per tonne to all plastic without a minimum of 30% recycled content.
DEFRA’s plans to bring in Extended Producer Responsibility legislation in 2024 will incentivise the industry’s supply chain to reduce its overall packaging output, especially plastic packaging, or to adopt recycled materials where a significant reduction in volume may not be possible.
Fleetwood says the audit has given NBG a much better understanding of where the problem areas are. “We will never be able to eliminate plastic packaging entirely, but the audit did identify areas for reduction," he said.
"There are clearly some products where it is entirely unnecessary to use plastic packaging, such as spades and other tools, or where it is for branding only, such as stone paving which is consolidated on wooden stillages.
“We also need to investigate alternative ways of securing products to a pallet other than stretch wrap.”
Fleetwood added that the audit did identify some major areas for concern. “We always knew stretch wrap would be a problem, but it was a surprise to find out that dumpy bags are a much bigger issue than we anticipated, accounting for approximately 27% of the audited merchant’s liability.
“We now need to accelerate the process of talking to our Suppliers about the feasibility of changing how they use plastic, without impacting product quality or safety during transportation.”
NBG has confirmed imminent plans to release guidance documents for Partners and Suppliers on how to navigate the financial obligations around plastic packaging.
Merchants and manufacturers wanting more information about NBG’s approach to plastic packaging should contact Jasmine King at jasmineking@nbgllp.com