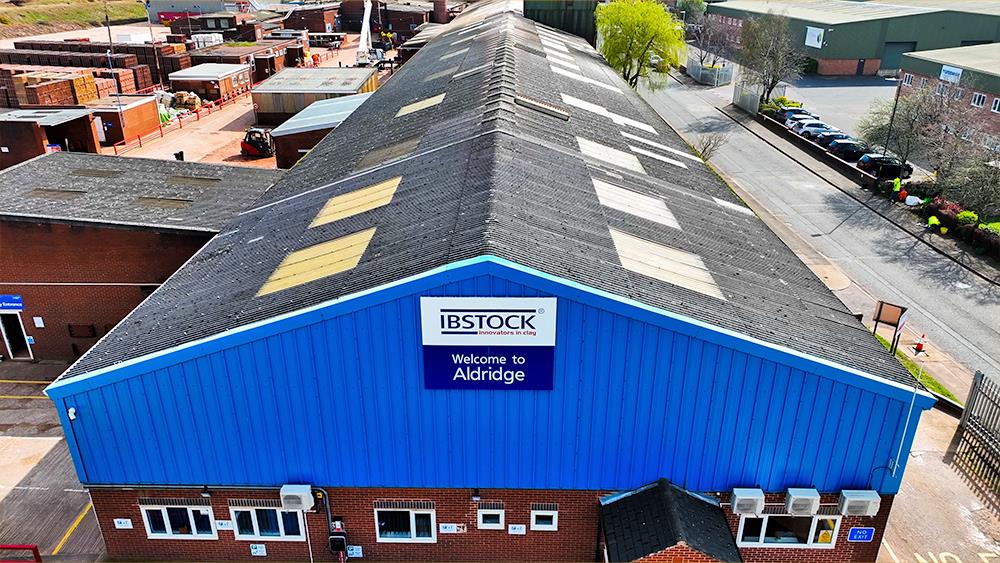
Ibstock has invested more than £12 million into its Aldridge factory – significantly improving energy efficiency and quality at the site.
As part of the investment, Ibstock has upgraded the legacy technology in the facility. This includes installing brand-new, state-of-the-art dryers, that feature screen-controlled moisture monitoring. This helps minimise surplus heat wastage, without compromising the final quality or durability of the bricks.
Similar upgrades have been made to the factory’s setting machine. Thanks to a new system that is largely automated, the setter can now process 10,000 bricks an hour – double the previous machine’s capabilities but requiring just one operator – helping to improve workflow and efficiency on site.
Further efficiency gains have been made via the introduction of an automated unpacking process, overseen by a team of three. This replaces the previous by-hand system, which was both time-consuming and labour-intensive.
The investment has also enabled a total refurbishment of the kiln cars and upgrades to the kiln itself, driving improvements in energy performance at the site. Upon completion of the investment, Ibstock expects gas consumption at the Aldridge site to be reduced by 25%, which equates to a total carbon reduction of 19%.
However, this investment has not only allowed Ibstock to make significant sustainability enhancements across the Staffordshire factory, it also drives real improvements to final product quality.
The improved efficiencies at Aldridge, coupled with its Midlands location, has helped Ibstock further sharpen its offering to the merchant sector. Aldridge is now able to supply a mixed load to merchants, ideal for branches with limited storage space – enabling merchants to purchase a variety of products from Ibstock and have everything delivered in one drop. What’s more, Aldridge bricks are now delivered in a bigger pack configuration (500 bricks per unit), helping merchants improve their stockholding.
Thanks to the upgrades to the site’s dryers and setting technology, Ibstock has been able to strengthen the quality of the bricks manufactured at Aldridge, improving production yield by10%.
Jason Grimston, Factory Manager at Aldridge, said: “As Factory Manager, it has been fantastic to see the impact the £12 million investment is having on our operations here at Aldridge. I’m not speaking in hyperbole when I say the funding has propelled the factory into a new era, where our 37-strong on-site team is now able to maximise its efficiency by using some truly state-of-the-art, semi-autonomous technology.
“At full demand, the factory will be able to produce up to 30 million bricks per year – ensuring we can guarantee a consistent supply to merchants and their end customers. Our commitment, however, doesn’t end at quantity; it’s about quality and sustainability, too. By upgrading the technology we’re using to manufacture our bricks, we’re able to ensure real consistency of quality for each and every brick that leaves the site.
“Indeed, with improved processes, we’re not just meeting standards – we’re setting new benchmarks for repeatability, consistency and aesthetic appeal. This investment is futureproofing Aldridge to ensure we remain best placed to meet changing customer demand and build a future where innovation and sustainability go hand in hand.”