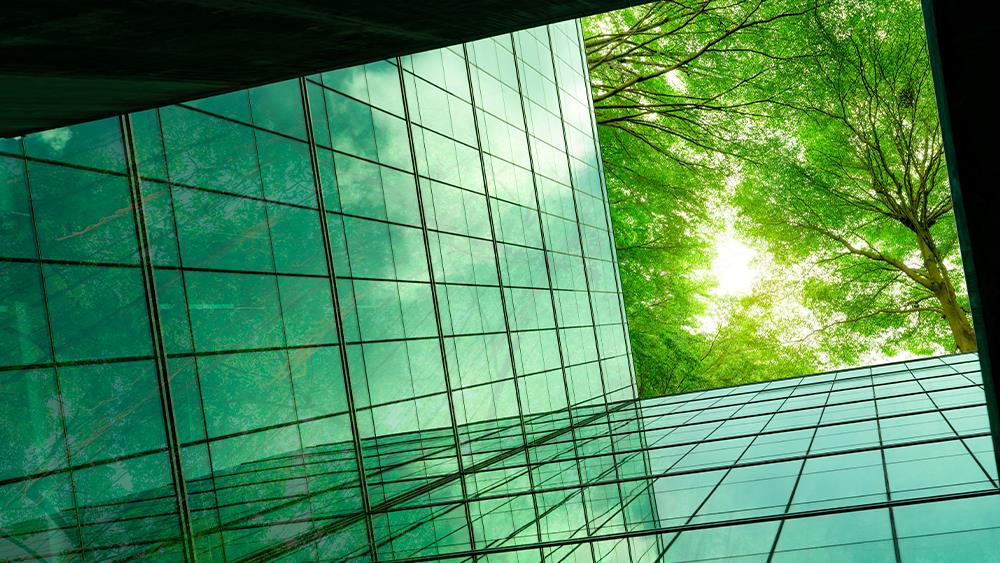
One of Britain’s largest contributors to climate change is at a turning point. The construction industry, responsible for 18% of the country’s large particle pollution, is now taking steps towards sustainability. But how soon can the industry realistically achieve this?
Digitising paper processes, working towards ISO 14001 and 50001, along with reviewing the supply chain are all simple steps towards decarbonisation that construction firms can start taking today. There’s also an increased urgency to deliver sustainability commitments across the sector.
Why must construction firms demonstrate their commitment to sustainability?
In light of the net zero targets set out by the UK government, and as a sector responsible for 40% of the UK’s carbon emissions, with 50m tonnes of CO2 produced every year, it is immediately clear why the industry must commit to sustainable targets.
Before 2030, the industry is expected to reduce its current emissions by at least 68%. The government has also made it clear that these targets are mandatory, especially for businesses bidding on government contracts worth over £5 million. To avoid being pushed out, businesses must act now.
Construction firms must therefore overhaul their processes and review any practices, contractors, goods, materials, or procedures that work against these targets. This could mean a greater investment in alternative-fuelled work vans and machinery as well as enhanced pressures on subcontractors to meet requirements.
What steps can construction businesses follow to improve sustainability?
Work to ISO 14001 and ISO 50001
Businesses aspiring to those high-ticket government contracts will need to highlight their dedication to reducing carbon emissions. They can achieve this by becoming accredited with ISO 14001 and ISO 50001. Those working towards ISO 14001 must outline carbon reduction targets for their organisation and determine a means to measure it.
There is no obligation for firms to become net zero immediately, but working towards an international standard solidifies the business’s commitment to sustainability. Likewise, ISO 50001 shows how firms are addressing their impact on the planet and resources.
Innovations in green building materials
The use of green building materials is a vital component of achieving sustainable construction. Those have been available for some time but the pressure to meet sustainability targets will make green materials more widely used.
Such materials, like recycled steel and low-VOC paints, for example, offer numerous advantages for firms looking to reduce their environmental impact. For instance, using recycled steel and concrete decreases the need for the resource-intensive manufacturing process to create them from scratch. Similarly, low-VOC paints are designed to promote a much healthier indoor air quality.
The trend towards better sustainability in the industry should also make green building materials more popular, with many users now choosing recycled or long-lasting materials over brand-new ones. As a result, the green building materials market is expected to grow to over £700 billion worldwide by 2033, leading to the further development of innovative and recyclable materials.
Energy-efficient design
This use of greener materials should be established from the drawing stage. Thanks to BIM (Building Information Modelling) software, architects and engineers can focus on energy-efficient designs whereby they visualise where greater energy efficiencies can be adopted. Expectations for sustainability can be set much earlier on in a development project.
Optimised supply chain
The emissions produced by subcontractors, the delivery of goods and import materials all count towards a construction firm's total emissions. That is why monitoring emissions and optimising the supply chain can immediately offer some reduction in those greenhouse gas emissions. This can be made easier by contractors and subcontractors also be producing their emissions reports in a bid to remain an attractive choice for projects.
Certain suppliers might use alternative-fuelled vehicles or follow more energy-efficient routes to complete deliveries. Likewise, for smaller projects, it could be more beneficial to source materials, services and goods within a local area, almost eradicating long delivery routes.
Review of internal processes
Leaving a physical paper trail behind can negatively impact emissions figures. Where possible, digitising certain paper-based procedures, such as goods received notes and invoicing, could work in favour of firms committed to reducing their greenhouse gas emissions.
In this case, using software, like a construction ERP system, can aid the process. Not only does it offer a futureproof solution for businesses needing to adapt quickly, but it also means productivity and efficiencies can be boosted too.
Switch to renewable energy
Transitioning to renewable energy is another way construction businesses can reduce their carbon emissions. Using solar, wind and geothermal power, construction projects can significantly reduce their reliance on fossil fuels, including gas, further demonstrating their commitment to the planet. Choosing renewable energy as part of an overall business strategy could also make firms more attractive for hire during the tender process.
Crossing the finish line: how construction firms can prepare for strict sustainability measures
From working towards ISO certifications to optimising the supply chain, there are plenty of opportunities for firms to invest in their business while exploring more sustainable pathways. With looming deadlines for both 2030 and 2050, imminent action is required. If the industry is to reduce 68% of emissions by 2030 and 100% of emissions by 2050, it is going to be a monumental task but one that could see businesses profit in the long run.